How Zirconia Sintering Furnaces Improve Dental Prosthetics
How Zirconia Sintering Furnaces Improve Dental Prosthetics
Blog Article
The globe of dental care has actually experienced a cutting edge change over the last few years, with dental CAD/CAM (computer-aided design/computer-aided production) innovation at the leading edge of this evolution. This high-tech advancement utilizes sophisticated software application and accurate equipment to layout and manufacture dental restorations, such as crowns, bridges, onlays, veneers, and inlays. Dental CAD/CAM milling burs are a necessary element in this process, playing a vital role fit complicated dental reconstructions with exceptional accuracy.
Milling burs are cutting devices used combined with dental milling makers to carve out and end up dental prosthetics from various products. These tools have to be sharp and incredibly resilient, offered the precision called for and the firmness of products they typically work with. Regular products include materials, porcelains, and metals, although progressively, zirconia has come to be the material of option for several dental remediations because of its exceptional toughness, biocompatibility, and aesthetic possibility.
Dental zirconia blanks, in some cases described as zirconia discs or blocks, are pre-manufactured forms of zirconia made use of in the milling process. Zirconia, a crystalline kind of zirconium dioxide (ZrO2), sticks out for its mechanical homes, which approach those of metals. These buildings include high crack toughness, resistance to use, and a shade that closely imitates all-natural teeth, making it ideal for dental applications. The manufacturing of dental zirconia starts with the formation of these blanks. They are made under high stress and temperature conditions, which convey superior thickness and mechanical attributes.
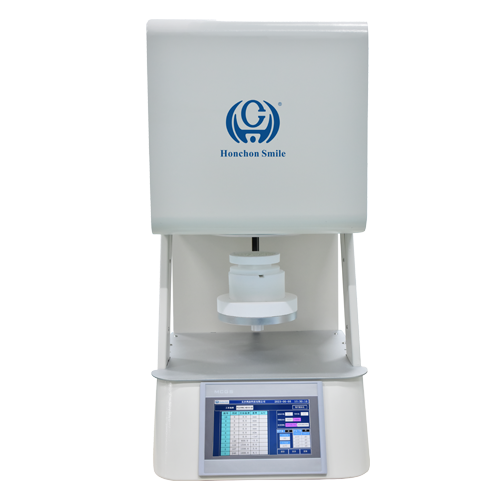
Discover the most recent innovations in dental CAD/CAM modern technology, zirconia milling, and 5-axis dental milling makers that are changing corrective dental care. Discover exactly how advancements like zirconia sintering furnace are improving individual, precision, and efficiency fulfillment in contemporary dental care.
As soon as the zirconia spaces are formed, they require to be sintered, normally in a zirconia sintering furnace. Sintering is a thermal process made to produce a strong mass from powder without melting it. During sintering, the zirconia bits fuse together at high temperature levels, improving the product's density and mechanical residential or commercial properties while attaining the desired clarity and shade gradients. A zirconia sintering furnace is a customized piece of equipment efficient in achieving the heats needed for this process, usually in the variety of 1350 ° C to 1600 ° C. The sintering procedure is vital, as it stabilizes the zirconia framework and secure its biocompatible and aesthetic high qualities.
Advanced milling devices, specifically 5-axis dental milling devices, have actually revolutionized the manufacturing of dental restorations. Generally, dental restorations needed labor-intensive processes and a substantial amount of time to create. The advancement to 5-axis technology has actually changed this significantly. Unlike 3-axis makers, which move in 3 linear axes (Y, x, and z), 5-axis makers include 2 additional rotational axes (A and B). This offers the milling machine the flexibility to come close to the zirconia blank from any angle, which is seriously essential for developing complex forms and damages precisely and effectively. The result is precision-crafted repairs that fit better, feel more comfortable, and look even more natural.
Additionally, current years have actually seen the intro of 3D plus Multilayer Blocks. These ingenious products incorporate the advantages of multi-layered zirconia with the precision of 3D printing technology. The multi-layered element describes the slope in shade and clarity within the zirconia block, mimicking the natural transition from dentin to enamel found in genuine teeth. This gradient impact is accomplished by layering various tones and levels of clarity of zirconia within the block throughout production. Subsequently, when this multi-layered block is milled, the resulting restoration looks a lot more realistic and calls for marginal post-processing or tarnishing to match the person's all-natural teeth.
3D printing technology has added an additional layer of modification and precision to this technique. By incorporating CAD/CAM styles with 3D printing, the complex information of the dental remediation can be caught and printed layer by layer. This results in even higher precision in fit and visual appeals, which is critical for patient satisfaction.
The mix of dental CAD/CAM systems, high-quality milling burs, dental zirconia spaces, sophisticated sintering heaters, 5-axis milling devices, and the most recent advancement in 3D plus Multilayer Blocks exemplifies the future of dental prosthetics. Dental specialists can give far better solution with quicker turnaround times, while people benefit from even more durable, better-fitting, and visually pleasing repairs.
As an example, the accuracy afforded by these technologies indicates prosthetics can be developed and made with a high level of precision, minimizing the need for repeated installations or changes. This degree of accuracy is mainly driven by the quality of dental CAD/CAM systems and making use of remarkable milling burs capable of fine detailing. Additionally, the handling of dental zirconia blanks in zirconia sintering heating systems ensures that the end product meets the greatest requirements of sturdiness and biocompatibility.
The advent of 5-axis dental milling makers has widened the range of what is possible in corrective dentistry. These equipments can mill complex geometries and great information which were not feasible prior to, paving the way for more advanced dental options.
On top of that, the continuous advancement in zirconia materials and CAD/CAM technologies perpetuates an extra effective and reliable dental treatment atmosphere. Dental practitioners can currently accomplish more predictable outcomes, decreasing chair time and enhancing person fulfillment. The extensive combination of these modern technologies right into routine dental method represents a seismic shift from reactive to proactive dental treatment, where digital perceptions, accurate milling, and prompt adjustments come to be basic technique.
By lowering product waste and enhancing the usage of sources, dental practices can operate a lot more sustainably. The international combination of these advanced materials and equipments right into dental educational program guarantees that future dental professionals are fluent in the latest technical breakthroughs, fostering a culture of continual renovation and advancement.
In recap, the harmony in between dental CAD/CAM systems, durable milling burs, high-grade zirconia blanks, efficient zirconia sintering furnaces, cutting edge 5-axis dental milling devices, and innovative 3D plus Multilayer Blocks is driving a brand-new age in dental care. This mix is transforming just how dental reconstructions are developed, made, and executed, bring about much better results for both dental professionals and clients. As modern technology remains to evolve, the future holds much more assurance for advancements that will even more reinvent dental treatment, making it a lot more precise, reliable, and patient-friendly than ever. Report this page